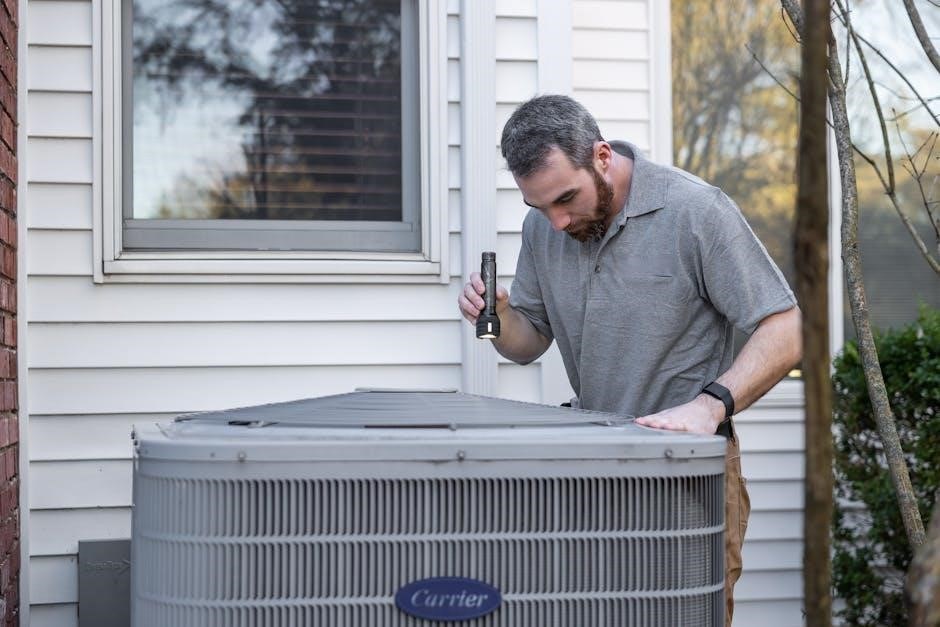
Refrigerant charging is a critical process in HVAC systems‚ ensuring efficient cooling and environmental compliance․ Proper procedures are essential for safety‚ system performance‚ and minimizing refrigerant emissions․
1․1 Importance of Proper Refrigerant Charging
Proper refrigerant charging is essential for ensuring optimal performance‚ efficiency‚ and longevity of air conditioning systems․ Incorrect charging can lead to reduced cooling capacity‚ increased energy consumption‚ and potential system damage․ Overcharging or undercharging can cause compressor strain‚ reduced reliability‚ and shortened equipment lifespan; Additionally‚ improper charging can result in refrigerant leaks‚ contributing to environmental issues and regulatory non-compliance․ Accurate refrigerant levels ensure safe operation‚ minimize emissions‚ and maintain system balance․ Technicians must adhere to established procedures to avoid these risks and guarantee efficient‚ eco-friendly‚ and safe system functioning․ Proper charging also prevents premature wear on components‚ reducing maintenance needs and extending system life․ It is critical to follow precise guidelines to achieve the correct refrigerant charge for optimal performance and environmental sustainability․
1․2 Safety Precautions and Protective Equipment
Safety is paramount during refrigerant charging and service procedures․ Technicians must wear protective gear‚ including safety goggles‚ gloves‚ and masks‚ to prevent exposure to refrigerants․ Refrigerants can cause skin irritation‚ respiratory issues‚ and eye damage upon contact․ Proper ventilation in the workspace is essential to avoid inhalation of refrigerant vapors․ Additionally‚ using approved recovery systems and storage tanks ensures compliance with environmental regulations and prevents refrigerant leaks․ Before starting any procedure‚ technicians should review the system’s service manual and ensure all safety protocols are followed․ Emergency equipment‚ such as spill kits and fire extinguishers‚ should be readily available․ Adhering to these precautions minimizes risks to personnel‚ the environment‚ and ensures safe‚ efficient servicing of air conditioning systems․ Safety measures are non-negotiable in maintaining a secure working environment and preventing accidents․
1․3 Overview of the Refrigerant Charging Process
The refrigerant charging process involves several key steps to ensure the system operates efficiently and safely․ First‚ the system must be evacuated using a vacuum pump to remove air‚ moisture‚ and contaminants․ This step is critical to prevent issues like ice formation and system damage․ Once the system is evacuated‚ it is essential to check for leaks to ensure there are no pathways for refrigerant to escape․ After confirming the system is leak-free‚ the refrigerant is charged according to the manufacturer’s specifications‚ either by weight or pressure readings․ The process may vary depending on the type of refrigerant‚ such as R-410A or R-22‚ and the system’s design․ Proper charging ensures optimal performance‚ energy efficiency‚ and environmental compliance․ Documentation of the refrigerant charge is also necessary for future reference and regulatory adherence․
Tools and Equipment Required for Refrigerant Charging
Key tools include manifold gauge sets‚ vacuum pumps‚ refrigerant scales‚ and leak detection tools‚ ensuring accurate and safe refrigerant charging and system maintenance․
2․1 Manifold Gauge Set
A manifold gauge set is essential for monitoring system pressure and temperature during refrigerant charging․ It includes low-pressure and high-pressure gauges‚ enabling precise control and diagnosis of system performance․ Proper use ensures accurate readings‚ preventing overcharging or undercharging‚ which can lead to inefficiency or system damage․ Technicians rely on these gauges to assess refrigerant flow and diagnose issues like leaks or blockages․ The manifold set connects to service ports‚ providing real-time data crucial for maintaining optimal operating conditions․ Regular calibration of the gauges is necessary to ensure accuracy and reliability in measurements․ This tool is indispensable for achieving the correct refrigerant charge‚ which is vital for system efficiency and environmental compliance․
2․2 Vacuum Pump
A vacuum pump is a critical tool for evacuating air and moisture from an HVAC system before refrigerant charging․ Proper evacuation ensures the system operates efficiently and prevents contamination․ The pump creates a vacuum‚ removing air‚ moisture‚ and other contaminants that could cause issues like ice formation or reduced performance․ It is essential to achieve the recommended vacuum level‚ typically below 500 microns‚ to ensure the system is dry and free of debris․ Using a vacuum pump also helps prevent refrigerant degradation and ensures accurate charging․ Regular maintenance of the pump is necessary to maintain its effectiveness․ Technicians rely on vacuum pumps to prepare systems for refrigerant charging safely and effectively‚ ensuring optimal system performance and longevity․
2․3 Refrigerant Scales
Refrigerant scales are essential tools for accurately measuring the amount of refrigerant charged into an HVAC system․ These scales ensure precise weighing‚ preventing overcharging or undercharging‚ which can lead to reduced efficiency or system damage․ Digital scales are preferred for their accuracy and ease of use‚ often featuring large displays and preset functions․ Scales must be calibrated regularly to maintain precision․ Technicians use them to monitor refrigerant levels during charging‚ ensuring compliance with environmental regulations and system specifications․ Proper use of refrigerant scales is vital for maintaining system performance‚ reducing emissions‚ and adhering to safety standards․ By accurately measuring refrigerant‚ scales help technicians optimize system operation and minimize potential environmental impact․ Regular calibration and maintenance of these scales are crucial for reliable and efficient refrigerant charging processes․
2․4 Leak Detection Tools
Leak detection tools are vital for identifying refrigerant leaks in HVAC systems‚ ensuring system efficiency and environmental compliance․ Common tools include electronic leak detectors‚ which use sensors to detect refrigerant traces‚ and ultraviolet (UV) dye kits‚ where dye is added to the refrigerant and detected using UV light․ Soap bubble solutions are also used for quick spot checks․ These tools help technicians locate leaks promptly‚ preventing refrigerant loss and potential system damage․ Regular inspections with these tools are essential for maintaining system performance and reducing emissions․ By identifying and addressing leaks early‚ technicians can ensure optimal cooling‚ minimize environmental impact‚ and extend equipment lifespan․ Proper use of leak detection tools is critical for effective refrigerant management and system reliability in air conditioning systems․
Preparing the Air Conditioning System for Refrigerant Charging
Preparing the system involves evacuating with a vacuum pump to remove moisture‚ checking for leaks‚ and connecting service ports for safe refrigerant charging․
3․1 Evacuating the System
Evacuating the system is a crucial step to remove air‚ moisture‚ and contaminants before refrigerant charging․ Using a vacuum pump‚ the system is depressurized to a minimum vacuum level to ensure all moisture is eliminated․ This prevents ice formation and system damage․ Proper evacuation ensures efficient operation and avoids potential malfunctions․ Always follow safety guidelines and manufacturer instructions during this process․ Regular maintenance of the vacuum pump is essential for optimal performance․
3․2 Checking for Leaks
Checking for leaks is a vital step before refrigerant charging to ensure system integrity․ Use electronic leak detectors or apply soapy water to joints and connections to identify escaping refrigerant․ Leaks can cause reduced efficiency‚ increased energy costs‚ and environmental harm․ Always perform leak checks after system servicing or repairs․ If a leak is detected‚ repair it immediately using appropriate sealants or replacing faulty components․ Neglecting leaks can lead to system failure and repeated refrigerant recharge․ Regular inspections help maintain optimal performance and compliance with environmental regulations․ Proper leak detection ensures a safe and efficient HVAC system operation․
3․3 Connecting Service Ports
Connecting service ports is essential for refrigerant charging and system maintenance․ Ensure the manifold gauge set is properly attached to the low-pressure and high-pressure ports․ Use service hoses with appropriate adapters to secure connections‚ avoiding cross-threading or damage․ Tighten all fittings to prevent refrigerant leaks․ Always wear safety goggles and gloves during this process․ Double-check the port labels to confirm correct connections‚ as incorrect hookups can lead to system damage or unsafe operating conditions․ Once connected‚ verify that all valves are in the correct position for charging․ Properly secured service ports ensure accurate pressure readings and safe refrigerant flow․ This step is critical for maintaining system efficiency and safety during charging procedures․
Step-by-Step Refrigerant Charging Procedures
Charging involves evacuating the system‚ connecting service ports‚ and adding refrigerant․ Use a vacuum pump to remove air and moisture‚ then measure and charge accurately for optimal performance․
4․1 Charging with R-410A Refrigerant
Charging with R-410A requires specific procedures due to its higher operating pressures compared to R-22․ Begin by evacuating the system using a vacuum pump to remove air and moisture․ Ensure the system reaches the recommended vacuum level to prevent contamination․ Once evacuated‚ connect the service ports and verify the system’s integrity․ Charge the refrigerant from the liquid phase of the cylinder‚ as vapor charging can lead to inaccurate measurements․ Use a manifold gauge set to monitor pressure levels‚ ensuring they align with the manufacturer’s specifications․ Always wear safety goggles and gloves during the process․ After charging‚ record the refrigerant amount on the service label and verify system performance․ Proper charging ensures energy efficiency and prevents environmental impact․ Follow manufacturer guidelines for optimal results․ Proper charging ensures energy efficiency and prevents environmental impact․ Follow manufacturer guidelines for optimal results․
4․2 Charging with R-22 Refrigerant
Charging with R-22 refrigerant involves specific steps to ensure system efficiency and safety․ Start by evacuating the system using a vacuum pump to remove air and moisture‚ ensuring the system is clean and dry․ Connect the service ports and verify their integrity before proceeding․ Use a manifold gauge set to monitor low and high-pressure sides‚ following manufacturer guidelines for optimal charging pressures; R-22 is typically charged in its vapor phase‚ so ensure the cylinder is in an upright position during the process․ Wear safety goggles and gloves to protect against potential hazards․ After charging‚ inspect the system for leaks and verify performance by checking superheat and subcooling levels․ Proper charging ensures the system operates efficiently while minimizing refrigerant emissions․ Always follow environmental regulations and use approved recovery systems if refrigerant removal is necessary․ Document the refrigerant charge level for future reference and compliance․
Charging with other refrigerant types‚ such as R-410A or newer alternatives‚ requires tailored procedures to match their unique properties․ Always refer to the manufacturer’s guidelines for specific instructions‚ as charging methods vary by refrigerant type․ For R-410A‚ ensure the system is compatible‚ as it operates at higher pressures than R-22․ Use the correct service equipment to avoid contamination and maintain system performance․ When charging‚ connect the refrigerant cylinder properly‚ ensuring it’s in the vapor phase for most systems․ Monitor system pressures using a manifold gauge set and adjust the charge based on superheat and subcooling levels․ Safety is paramount; wear protective gear and follow environmental regulations for handling refrigerants․ Proper charging ensures optimal efficiency‚ reduces emissions‚ and complies with industry standards․ Document the process and refrigerant type used for future maintenance and compliance purposes․ Always verify system performance post-charging to ensure correct operation․ Accurate measurement ensures optimal system performance․ Use manifold gauges to monitor pressure and calculate superheat/subcooling․ Adjust the charge to match manufacturer specifications for efficiency and reliability․ Manifold gauges are critical tools for measuring refrigerant pressure and temperature during charging․ They consist of three hoses: low-pressure (blue)‚ high-pressure (red)‚ and a yellow service hose for adding refrigerant․ Always wear safety goggles and gloves when operating gauges․ Connect the hoses to the system’s service ports and monitor pressures to diagnose issues․ Use the gauge readings to calculate superheat and subcooling‚ ensuring the charge matches the manufacturer’s specifications․ For R-410A and R-22 systems‚ follow specific procedures to avoid overcharging or undercharging․ Proper use of manifold gauges ensures efficient system performance‚ prevents damage‚ and minimizes refrigerant emissions․ Refer to the system’s service manual for detailed connection and operation guidelines to maintain safety and accuracy during the charging process․ Measuring superheat is crucial for ensuring proper refrigerant charging․ Superheat is the difference between the refrigerant’s actual temperature and its saturation temperature at a given pressure․ To measure superheat‚ use manifold gauges to determine the pressure at the evaporator inlet․ Convert this pressure to a temperature using a pressure-temperature chart․ Subtract the saturation temperature from the refrigerant’s actual temperature to find the superheat value․ Proper superheat levels‚ typically between 8°F to 12°F‚ ensure efficient operation and prevent system damage․ Adjust the refrigerant charge if superheat is outside this range․ Always refer to the manufacturer’s guidelines for specific recommendations․ Measuring subcooling ensures the refrigerant is properly cooled before entering the expansion valve․ Subcooling is the difference between the refrigerant’s actual temperature and its saturation temperature at the condenser’s outlet․ To measure subcooling‚ use manifold gauges to determine the pressure at the condenser outlet․ Convert this pressure to a temperature using a pressure-temperature chart․ Subtract the saturation temperature from the refrigerant’s actual temperature to find the subcooling value․ Typical subcooling ranges are 5°F to 10°F․ Adjust the refrigerant charge if subcooling is outside this range․ Proper subcooling prevents liquid refrigerant from entering the compressor‚ reducing efficiency and potentially causing damage․ Always follow manufacturer guidelines for specific systems to ensure optimal performance and reliability․ Common issues include low refrigerant charge‚ overcharging‚ and refrigerant leaks․ Identifying these problems early ensures system efficiency and prevents damage․ Always follow diagnostic procedures carefully․ A low refrigerant charge can lead to reduced cooling performance‚ increased energy bills‚ and potential system damage․ Symptoms include reduced airflow‚ ice buildup on coils‚ and warm air from vents․ Compressors may overheat‚ and the system may cycle frequently․ Technicians should inspect for leaks‚ check pressure levels‚ and verify proper evacuation procedures․ Early detection prevents costly repairs and ensures optimal system operation․ Always follow diagnostic guidelines to identify and address low charge issues effectively․ Overcharging refrigerant can cause system inefficiency‚ increased energy consumption‚ and potential component damage․ Symptoms include excessive compressor noise‚ higher operating pressures‚ and reduced cooling performance․ The system may experience decreased airflow‚ increased humidity levels‚ and frost buildup on the evaporator coil․ Overcharging can also lead to refrigerant leaks and premature wear on compressors and expansion valves․ Technicians should monitor pressure levels‚ check for excessive refrigerant flow‚ and ensure proper charging procedures․ Addressing overcharging promptly prevents long-term damage and maintains system efficiency․ Refrigerant leaks are a common issue that can significantly impact system performance and environmental compliance․ Leaks lead to reduced cooling capacity‚ increased energy consumption‚ and potential system damage․ They also contribute to ozone depletion and climate change by releasing harmful refrigerants into the atmosphere․ Common signs of leaks include hissing sounds‚ visible frost on pipes‚ and low refrigerant pressure levels․ Technicians must identify and repair leaks promptly to ensure system efficiency and compliance with environmental regulations․ Proper leak detection tools‚ such as electronic detectors or dye injection‚ are essential for accurate diagnosis․ Addressing leaks ensures optimal system operation and minimizes environmental impact․ Documentation and compliance are crucial in HVAC maintenance․ Proper recording of refrigerant charge levels ensures environmental adherence․ Non-compliance can result in fines and legal action․ Accurate documentation of refrigerant charge levels is essential for system performance and compliance․ Technicians must record the amount of refrigerant added‚ the date‚ and system specifications․ This ensures accountability and traceability‚ aiding in future maintenance and audits․ Proper records help verify that the system operates within designed parameters‚ optimizing energy efficiency and preventing overcharging or undercharging․ Additionally‚ documentation supports compliance with environmental regulations‚ such as the Clean Air Act‚ and helps track refrigerant emissions․ Service labels on units should include refrigerant type‚ charge amount‚ and other critical details․ Maintaining detailed records also assists in identifying potential leaks or irregularities‚ ensuring system reliability and environmental sustainability over time․ Environmental regulations mandate strict adherence to refrigerant handling practices to minimize ecological impact․ Technicians must comply with standards set by agencies like the EPA‚ ensuring proper recovery‚ recycling‚ and disposal of refrigerants․ The Clean Air Act prohibits venting refrigerants‚ requiring the use of approved recovery systems․ Proper charging and leak detection are critical to prevent emissions․ Additionally‚ technicians must obtain certifications‚ such as EPA Section 608‚ to handle refrigerants legally․ Compliance also involves accurate record-keeping of refrigerant usage and disposal‚ aiding in audits and accountability․ Adhering to these regulations helps protect the ozone layer and mitigate climate change by reducing greenhouse gas emissions․ Staying informed about updates to environmental laws ensures ongoing compliance and sustainable practices in HVAC service procedures․ Optimizing refrigerant charge and ensuring proper system maintenance are key to maximizing energy efficiency․ Using inverter technology and smart controls can further reduce energy consumption in HVAC systems․ Optimizing refrigerant charge is vital for energy efficiency in HVAC systems․ Proper charging ensures the system operates within design parameters‚ reducing energy consumption and enhancing performance․ Overcharging or undercharging can lead to inefficiency‚ increased energy bills‚ and potential system damage․ Technicians should use manifold gauges to measure superheat and subcooling accurately‚ ensuring the refrigerant level matches manufacturer specifications․ Regular maintenance‚ such as checking for leaks and ensuring proper evacuation‚ also plays a crucial role in maintaining optimal charge levels․ By adhering to best practices‚ technicians can maximize system efficiency‚ reduce environmental impact‚ and provide reliable cooling performance for users․ Proper refrigerant management is essential for sustainable and energy-efficient HVAC operation․ Reducing refrigerant emissions is critical for environmental protection and compliance with regulations․ Proper evacuation and charging procedures minimize refrigerant release during servicing․ Using leak detection tools ensures systems are tight‚ preventing gradual emissions․ Recovery systems are essential for capturing refrigerant during repairs or decommissioning‚ avoiding illegal venting․ Regular maintenance‚ such as inspecting service ports and hoses‚ reduces potential leaks․ Technicians should follow best practices‚ like using vacuum pumps to remove moisture and air before charging‚ to prevent contamination and overcharging․ Properly labeling systems with refrigerant types and charge levels aids in accurate servicing․ Training and certification programs ensure technicians adhere to environmentally responsible practices․ Reducing emissions not only protects the ozone layer but also mitigates climate change by minimizing greenhouse gas releases․ Compliance with environmental regulations is both a legal and ethical responsibility in the HVAC industry․ The transition to eco-friendly refrigerants like R-410A and new blends is expected to dominate the industry․ Advances in charging technology‚ such as automated systems and smart sensors‚ will enhance efficiency and reduce emissions‚ aligning with global sustainability goals․ The HVAC industry is shifting toward environmentally friendly refrigerants due to global regulations and environmental concerns․ Refrigerants like R-410A and R-32 are replacing older types such as R-22‚ which contribute to ozone depletion and climate change․ These newer refrigerants have lower global warming potential (GWP) and are more energy-efficient․ The transition requires updated tools‚ training‚ and service procedures to handle the unique properties of these refrigerants․ Technicians must adapt to these changes to ensure compliance with environmental regulations and to meet the demand for sustainable cooling solutions․ Proper handling and charging procedures for new refrigerant types are critical to maintain system performance and reduce emissions․ Modern advancements in refrigerant charging technology are enhancing efficiency and accuracy․ Automated charging systems now use sensors and digital controls to measure and inject the precise amount of refrigerant‚ reducing human error․ Smart systems integrate with manifold gauges and vacuum pumps‚ enabling real-time monitoring and data logging․ These technologies improve charging precision‚ reduce waste‚ and comply with environmental standards․ Additionally‚ wireless connectivity and mobile apps allow technicians to access charging data remotely‚ streamlining service procedures․ These innovations not only improve the reliability of HVAC systems but also support the transition to new refrigerant types‚ ensuring a sustainable future for air conditioning and refrigeration industries․4․3 Charging with Other Refrigerant Types
Measuring and Adjusting Refrigerant Charge
5․1 Using Manifold Gauges
5․2 Measuring Superheat
5․3 Measuring Subcooling
Troubleshooting Common Refrigerant Charging Issues
6․1 Low Refrigerant Charge Symptoms
– Reduced cooling capacity
– Increased energy consumption
– Ice formation on evaporator coils
– Compressor overheating
– Frequent system cycling
– Warm air discharge6․2 Overcharging Refrigerant Symptoms
– Increased operating pressures
– Reduced system performance
– Higher energy consumption
– Excessive compressor noise
– Potential for refrigerant leaks
– Decreased airflow and cooling capacity6․3 Refrigerant Leaks and Their Impact
– Reduced system efficiency
– Environmental harm
– Increased energy costs
– Potential for system damageDocumentation and Compliance
7․1 Recording Refrigerant Charge Levels
7․2 Compliance with Environmental Regulations
Best Practices for Energy Efficiency
8․1 Optimizing Refrigerant Charge for Efficiency
8․2 Reducing Refrigerant Emissions
Future Trends in Refrigerant Charging
9․1 Transition to New Refrigerant Types
9․2 Advances in Charging Technology